Understanding Manifold Valve Assembly: A Comprehensive Guide
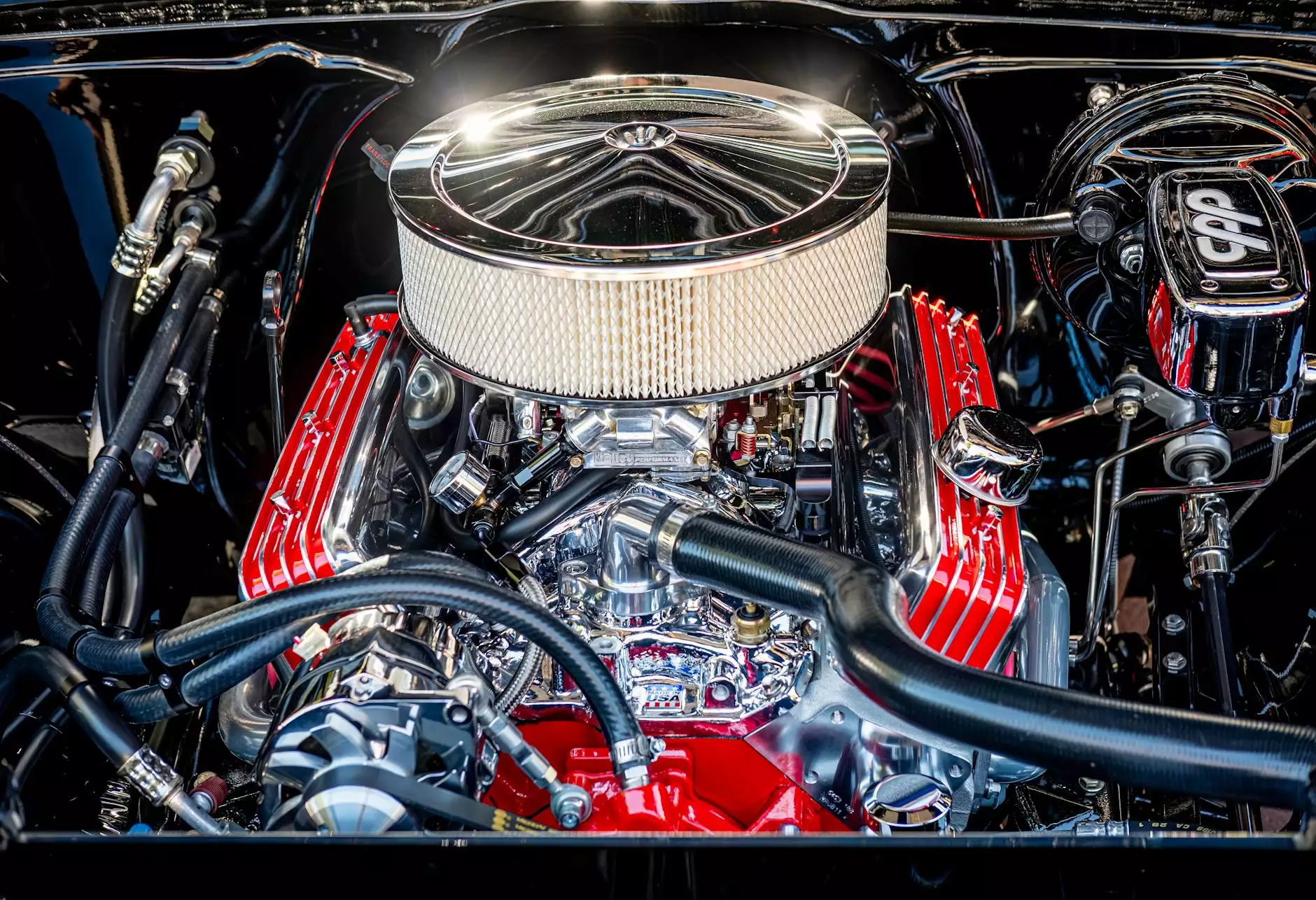
In the dynamic world of industrial applications, the importance of reliable components cannot be overstated. Among these components, the manifold valve assembly plays a pivotal role in managing fluid flow and pressure across various systems. This article delves into the intricacies of manifold valve assemblies, revealing their types, functions, applications, and why they are essential for optimal system performance.
What is a Manifold Valve Assembly?
A manifold valve assembly is a sophisticated component that consolidates several valve functions into a single manifold. This assembly allows multiple circuits to be controlled from one location, improving efficiency and simplifying installation. The valve assembly typically consists of various valves, including check valves, ball valves, and needle valves, each serving a specific purpose within a fluid handling system.
Components of a Manifold Valve Assembly
The manifold valve assembly is composed of several integral parts, each designed to ensure precise control of fluid flow:
- Valves: The core of the assembly, which includes check valves, ball valves, and needle valves.
- Body: The main structure that houses the valves and provides the necessary connections to piping systems.
- Ports: Inlets and outlets for connecting to various lines or instrumentation.
- Seals and Gaskets: Essential for preventing leaks and maintaining system integrity.
- Actuators: Optional components that automate the opening and closing of valves, enhancing system control.
Types of Manifold Valve Assemblies
Understanding the different types of manifold valve assemblies is key to selecting the right component for specific applications:
- Pressure Manifold Valve Assembly: Designed to manage high-pressure systems, these assemblies ensure that pressure is regulated optimally for safe operation.
- Instrument Manifold Valve Assembly: Used in instrumentation applications to isolate pressure sensors and transmitters.
- Utility Manifold Valve Assembly: Commonly found in installations requiring rapid alterations in flow, such as HVAC systems.
- Hydraulic Manifold Valve Assembly: Tailored for hydraulic systems, these assemblies regulate the flow of hydraulic fluids with precision.
Applications of Manifold Valve Assemblies
The versatility of manifold valve assemblies makes them applicable in various industries:
1. Oil and Gas Industry
In the oil and gas sector, these assemblies regulate flow, ensuring safe operations in extraction and distribution processes. Proper management of pressure and flow prevents hazardous situations and equipment failures.
2. Chemical Processing
Chemical facilities utilize manifold valve assemblies to manage the intricate flow of various chemicals, ensuring precise control over reactions and safety measures to prevent mixture hazards.
3. Water Treatment Systems
In water treatment, manifold valve assemblies streamline the distribution of treated and untreated water, improving the efficacy of purification processes while providing necessary control.
4. HVAC Systems
Heating, Ventilation, and Air Conditioning (HVAC) systems rely on manifold valve assemblies to control fluid dynamics for temperature regulation and air quality management, improving energy efficiency.
Benefits of Manifold Valve Assemblies
Utilizing a manifold valve assembly presents numerous advantages:
- Space Efficiency: Consolidating multiple valves into a single assembly saves valuable space in complex systems.
- Improved Safety: By centralizing control, operators can quickly isolate sections of a system, enhancing safety protocols.
- Reduced Installation Time: Fewer components translate to quicker installation, resulting in lower labor costs and faster operational capabilities.
- Enhanced Maintenance: Easier access to controls and components leads to simplified maintenance routines.
Choosing the Right Manifold Valve Assembly
Selecting the appropriate manifold valve assembly requires consideration of several factors:
1. Application Requirements
Understanding the specific needs of your application, such as pressure ranges and fluid types, is crucial for selecting a suitable manifold assembly.
2. Material Compatibility
Ensure that the materials used in the manifold assembly are compatible with the fluids being handled to prevent corrosion and material degradation.
3. Size and Flow Rate
Assess the flow requirements to choose a manifold valve assembly that can handle the necessary flow rate for your system efficiently.
4. Automation Needs
If automated control is required, consider assemblies that incorporate actuators for remote operation.
Maintenance of Manifold Valve Assemblies
Regular maintenance of manifold valve assemblies is vital for ensuring long-term performance:
1. Routine Inspections
Schedule regular inspections to identify any signs of wear or leaks which may indicate the need for repairs or replacements.
2. Cleanliness
Keep the assembly clean and free from debris to prevent damage to the valving and sealing surfaces.
3. Lubrication
Proper lubrication of moving parts helps reduce friction and prolongs the lifespan of the assembly.
4. Testing
Implement periodic testing to evaluate the functionality of the valves, ensuring that they operate correctly under various conditions.
Conclusion
In summary, the manifold valve assembly is a fundamental component in numerous industrial applications, providing enhanced control, efficiency, and safety. Understanding its types, applications, and the intricacies of selecting and maintaining these assemblies equips businesses to optimize their operations. If you are looking for high-quality manifold valve assemblies to integrate into your systems, explore the offerings at TechTubes, a leader in the industry.
Your operational success hinges on the reliability of components like manifold valve assemblies. Investing in quality is essential for maintaining the efficiency and safety of your systems, paving the way for sustainable industrial growth.